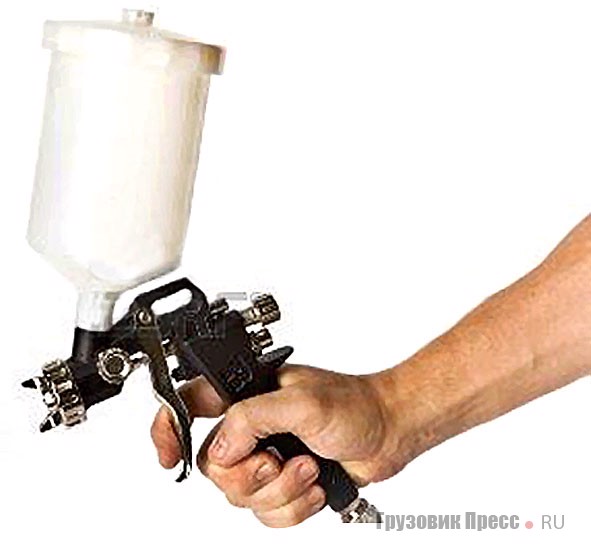
Чем красят автомобильные кузова?
Чем красят автомобильные кузова? Ответ на этот вопрос в разное время звучит по-разному…
Что происходит на конвейере
Прежде всего договоримся о терминологии. Если говорить о процессе нанесения лакокрасочных материалов (ЛКМ), как будет правильно: «покраска кузова» или «окраска»?
Филолог проголосует за покраску. Мол, окраска – это приобретённое свойство, полученный цвет. Вспомнит защитную окраску у хамелеона и тому подобные примеры. А применительно к технологии надо говорить «покраска». С ним не согласится автомобильный маляр: окраска, и все тут. Так пишут в профессиональных статьях. И он привык говорить так же. Мы принимаем сторону маляра и переходим к теме.
Итак, окраска кузова… На конвейере кузова и кабины «в металле» тщательно обезжиривают, промывают и направляют в огромную ванну для химической обработки – фосфатирования. После этой операции на металлической поверхности образуется тончайшая плёнка из фосфатов железа и цинка, назначение которой – защищать металл от коррозии при появлении микротрещин в будущих слоях лакокрасочных материалов. Отметим, что фосфатная плёнка обладает хорошей адгезией к металлу и обеспечивает надёжную адгезию последующих защитных слоев.
![[b]Слои, наносимые на металл, используемые в производстве коммерческих автомобилей конвейерным способом:[/b] 1 – фосфатная плёнка; 2 – пассивирование цинкового или хромного покрытия; 3 – катафорезный слой; 4 – выравнивающая грунтовка; 5 – базовая эмаль; 6 – прозрачный лак](/article/25775-chem-krasyat-avtomobilnye-kuzova-evolyutsiya-emaley/Images/01.jpg)
После фосфатирования кузов снова тщательно промывают, сушат и… опять погружают в гигантскую ванну. В этой ёмкости на фосфатную пленку методом катодного или анодного осаждения наносят слой водоразбавляемой грунтовки с антикоррозионными добавками.
Если кузов служит катодом, процесс именуется катафорезом, в противном случае – анафорезом. Отметим, что катафорез обеспечивает более надёжную антикоррозионную защиту, поэтому анафорез сегодня практически не применяют. Толщина слоя катафорезной грунтовки достигает 20 мкм, а благодаря электроосаждению он распределяется равномерно как на горизонтальных, так и на вертикальных поверхностях, включая скрытые полости кузова и сварные швы.
После сушки при 180 °С на катафорезный слой наносят еще одну грунтовку – выравнивающую. Ее назначение двояко: во-первых, заполнять и сглаживать мелкие дефекты поверхности, во-вторых, ограничивать развитие трещин в будущем лакокрасочном слое. К слову, в отличие от катафорезной, выравнивающая грунтовка от коррозии не защищает.
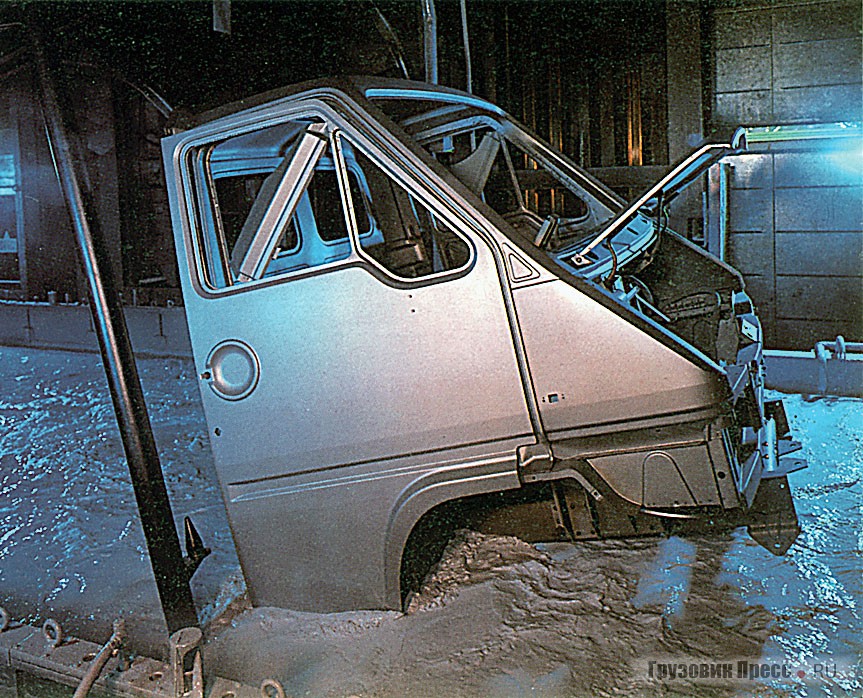
И, наконец, после сушки и шлифования загрунтованная поверхность окрашивается эмалью либо материалами двухслойной системы: базовая эмаль (металлик) плюс прозрачный лак.
Существуют конвейерные технологии, где выравнивающая грунтовка отсутствует. В этом случае применяется особое катафорезное грунтование с толщиной слоя до 40 мкм. Требования к качеству металла и к качеству сборки кузова здесь очень высокие! Зато выигрыш налицо: экономятся производственные площади и энергозатраты на сушку, а также сокращаются выбросы в атмосферу летучих органических соединений (ЛОС). Иногда выравнивающую грунтовку заменяют дополнительной базисной эмалью, при этом она выполняет две функции – выравнивания и создания черного или белого цветового подслоя для получения специальных эффектов в трехслойных системах ЛКМ.
Мы совершили краткий экскурс, чтобы напомнить: даже самые современные автоэмали не обеспечат качественную окраску кузова без тщательной его подготовки – и конвейерные технологии иллюстрируют это как нельзя лучше.

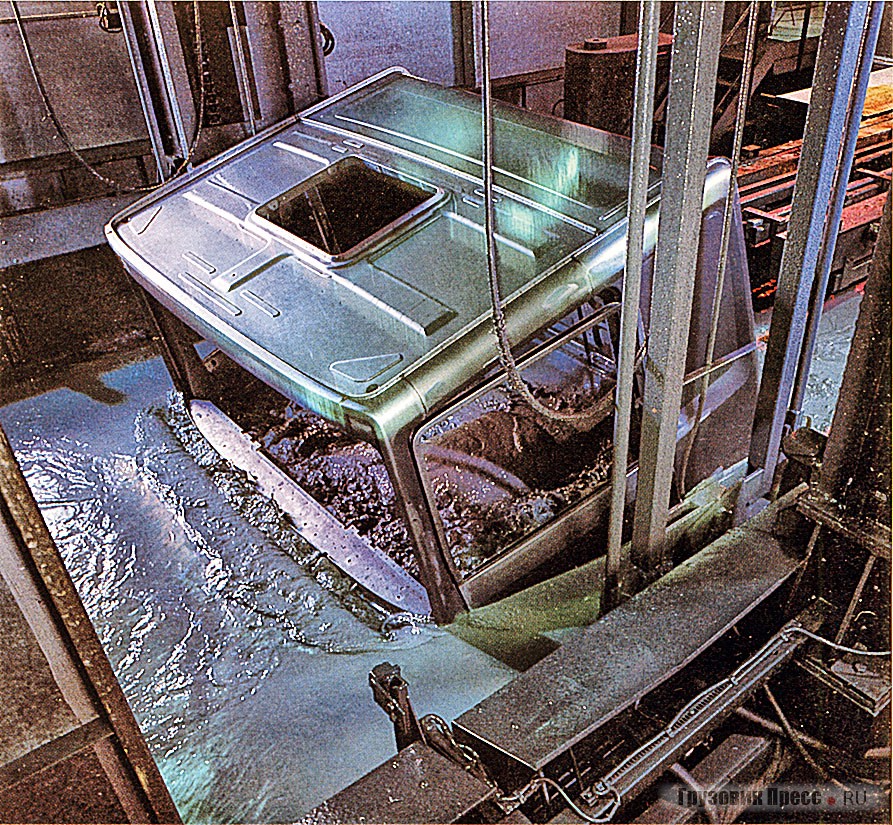
Нитроэмали
На заре автомобилестроения маляры использовали краски на основе природных смол, скипидара и олифы с добавками сажи и других пигментов. В двадцатые годы на смену таким краскам пришла нитроэмаль.
После окончания Первой мировой войны производственные мощности по выпуску пороха оказались незагруженными. Но химики быстро сообразили: пироксилин (тринитрат целлюлозы), применяемый в производстве пороха, и коллоксилин, идущий на изготовление нитролака – близнецы-братья! И тот, и другой являются сложными эфирами целлюлозы и азотной кислоты и различаются, в частности, содержанием азота. И вот многие пороховые заводы занялись выпуском киноплёнки, а также нитролаков и нитроэмалей на основе нитроцеллюлозы.
Напомним о некоторых свойствах нитроэмалей. Низкое содержание нелетучих веществ в растворе коллоксилина определяет малую толщину плёнки при высыхании, поэтому для получения качественного покрытия толщиной 75–125 мкм требуется наносить до десяти слоев эмали. Готовое покрытие стойко к действию температур в диапазоне от –40 до +60 °С. Если же нитроэмалевое покрытие нагреть до 100 °С и более, плёнка разрушится и даже может загореться.
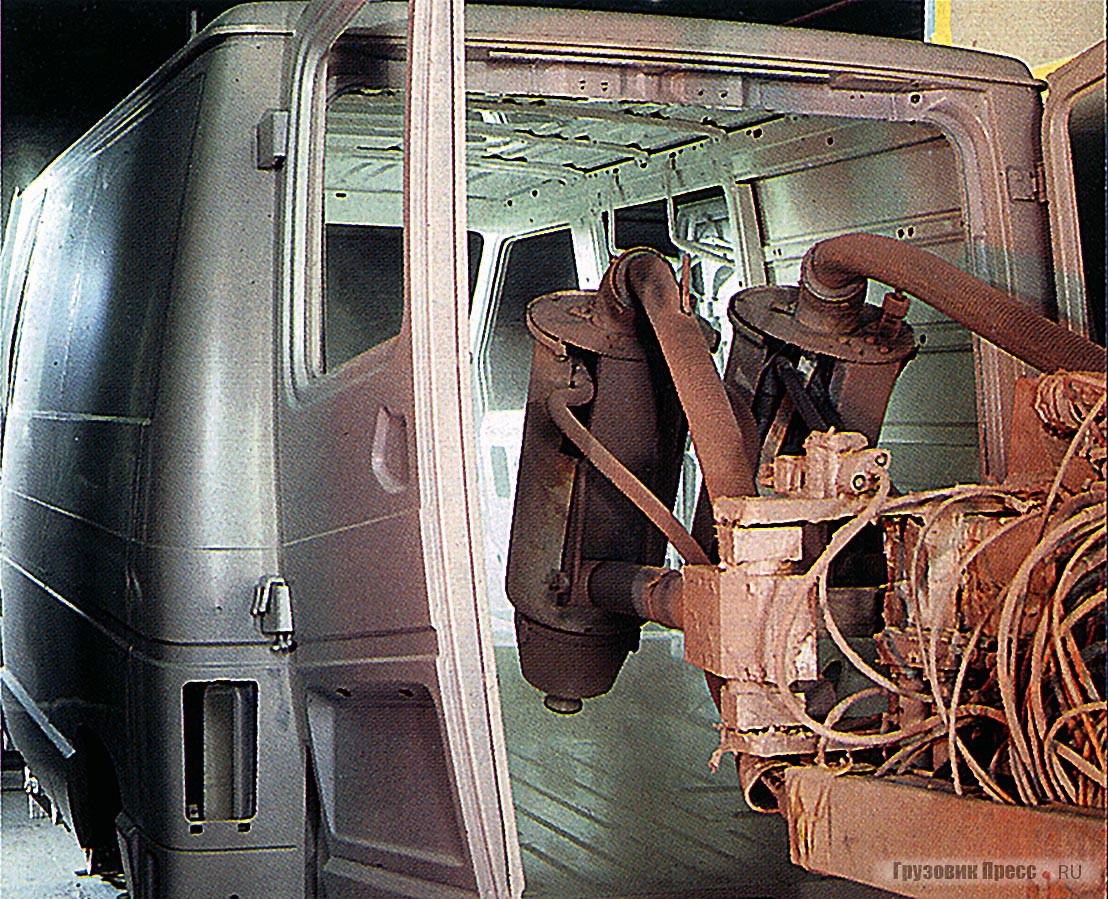
Иногда спрашивают: за счёт чего происходит полимеризация нитроэмали? Запомним раз и навсегда: никакой полимеризации в нитроэмалях не происходит! Отверждение, а точнее высыхание, осуществляется за счет испарения летучих растворителей. Это чисто физический процесс. После высыхания образуется обратимая плёнка, которая может быть снова растворена в растворителе.
Для своего времени нитроэмали были, безусловно, хороши: они быстро высыхали при комнатной температуре и неплохо противостояли воздействию масел, бензина, солнечных лучей и атмосферных осадков. Правда, для сохранения высокого блеска они требовали частой полировки, но с этим приходилось мириться.
В советские времена правительственные ЗИЛы и «Чайки» окрашивали только нитроэмалями. Покрытия насчитывали до 12 слоёв, включая грунтовочные, и выглядели те «членовозы» великолепно. Правда, их почти непрерывно подкрашивали и полировали – благо было кому…
Под маркой НЦ нитроэмали выпускаются и по сей день. В сегодняшнем кузовном ремонте они применяются крайне редко, что неудивительно: по всем показателям, кроме цены, нитроэмали проигрывают современным ЛКМ. Мы же относимся к этим материалам с искренним уважением – все же они были первыми!
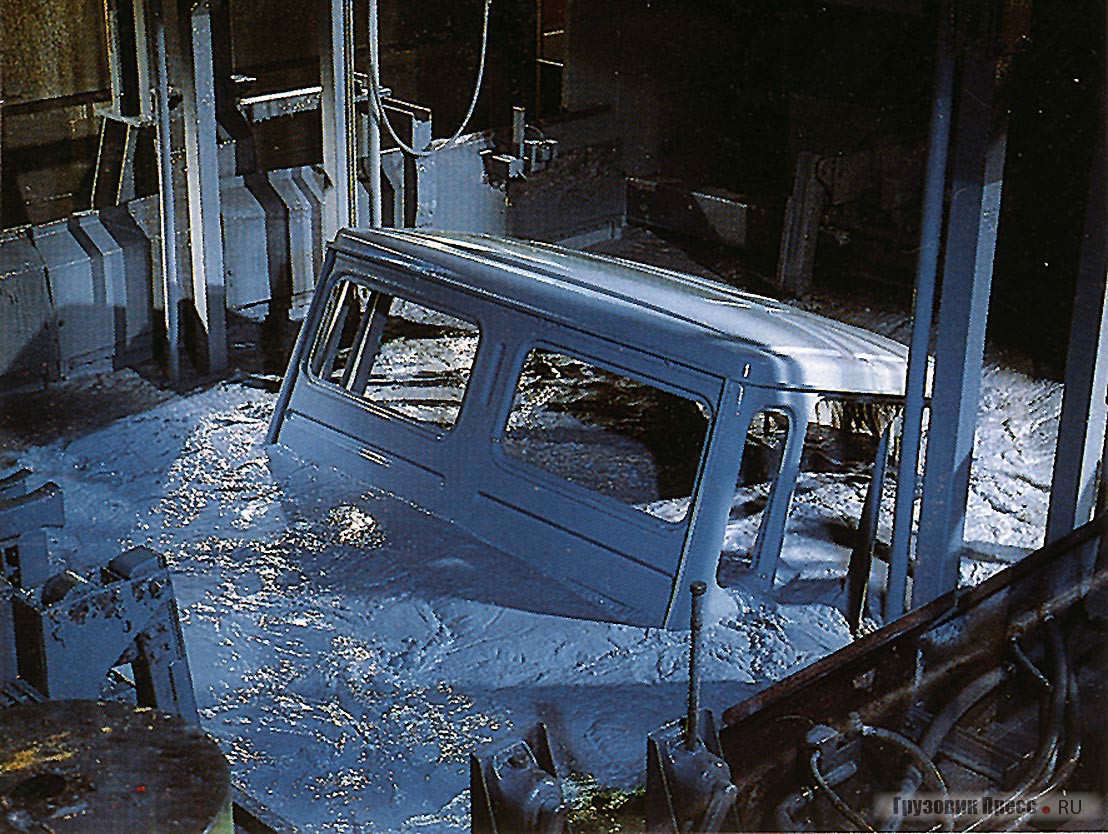
Алкидные эмали
Их у нас называют «эмалями воздушной сушки» – и вполне справедливо, о чем будет сказано далее. А пока несколько формальностей.
Алкидная эмаль – это суспензия пигментов в алкидных лаках с добавками модификаторов – в частности, растительных масел. И тут возникает закономерный вопрос: а что такое алкидные лаки? Пожалуйста, это растворы алкидных смол. Хорошо, а что такое «алкидные смолы»? Слово «алкидный» происходит от англ. alcohol – спирт и acid – кислота. Соответственно алкидные смолы получают на основе многоатомных спиртов и многоосновных кислот. Попутно заметим, что термина «алкид» в фундаментальной химии не существует, это термин из лексикона лакокрасочников.
К алкидным относятся и некоторые ремонтные автоэмали. Возможно, кто-то удивится: неужели ПФ-115 и звучные брендовые продукты стоят в одном ряду? Да, с точки зрения механизма отверждения это так. В отличие от нитроэмалей при сушке алкидных материалов параллельно протекают два процесса: испарение растворителя (физическая сушка) и химическое превращение компонентов связующего в пространственно-сшитый полимер. После полного отверждения растворить такую пленку невозможно, поэтому ее называют необратимой.
В банке с алкидной эмалью находится один компонент, способный к реакции, – это раствор алкидной смолы, модифицированный растительным маслом. От растительного масла продукту достаются «хвосты» высших жирных непредельных кислот, содержащих сопряженные двойные связи.
Второй компонент алкидных эмалей – это кислород воздуха. Благодаря его взаимодействию с указанными двойными связями образуется высокомолекулярное соединение, т. е. происходит отверждение. А поскольку каждая молекула алкидного компонента имеет несколько двойных связей, полимер получается «пространственно сшитым». Так что кислород – полноценный компонент связующего, его вполне можно считать отвердителем.
Маляры знают, что плёнка алкидной эмали хорошо сохнет сверху, а вот «вглубь» – хуже… Это характерно при отверждении кислородом – по мере высыхания его доступ вглубь слоя затрудняется. Поэтому задача производителя – применение технических решений, обеспечивающих равномерноe высыхание плёнки. А на совести автомаляра – делать покрытие равномерным по толщине.
Авторемонтные алкидные эмали конечно же имеют более высокое качество по сравнению с «дачной» ПФ-115. И сегодня на рынке есть очень неплохие алкидные авторемонтные эмали российского производства. Они еще послужат владельцам отечественных грузовиков и автобусов, особенно при весеннем обновлении внешнего вида. На конвейерах алкидные эмали не применяются.
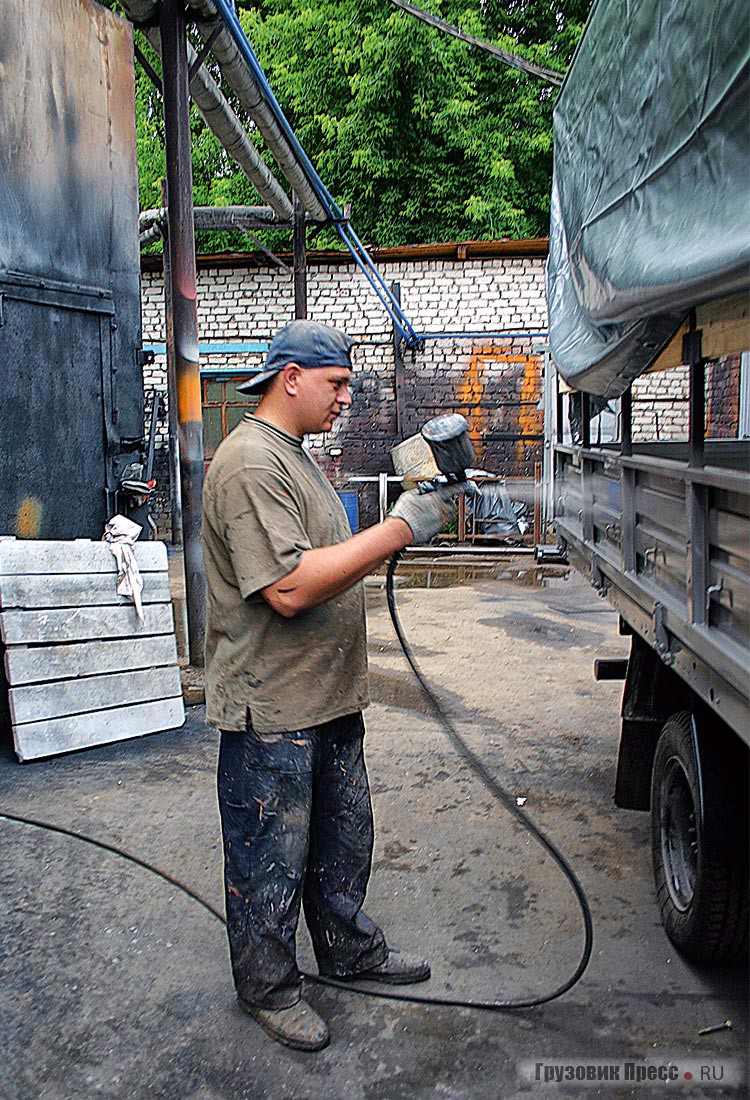
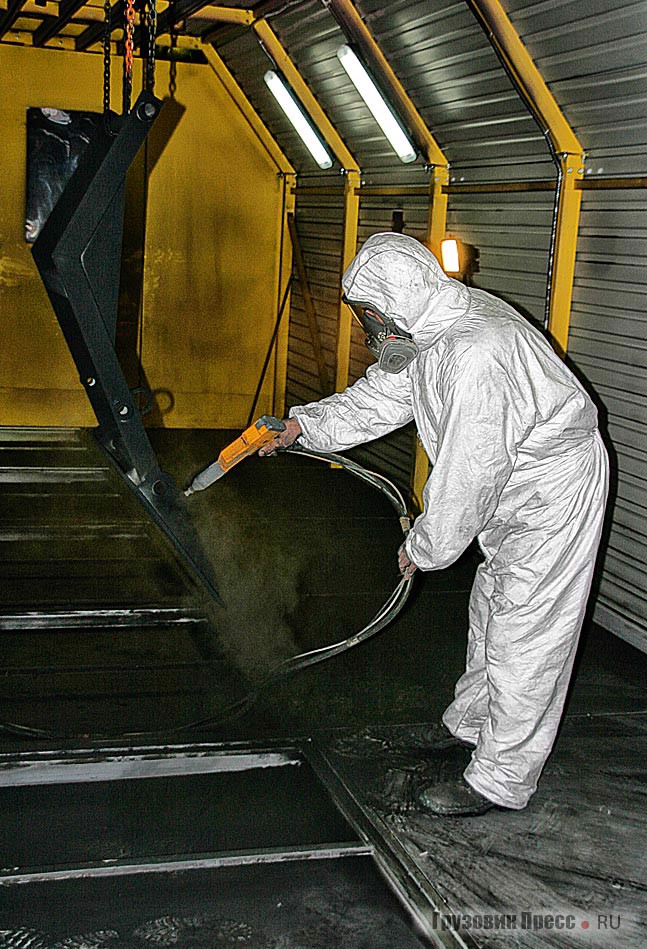
Меламиноалкидные эмали
Наши мастера давно и упорно называют их «синтетикой». Почему? Никакого секрета: при создании алкидной части этих эмалей химики использовали синтетические жирные кислоты. Отсюда и пошло – «синтетика», «окрасить синтетикой».
Как и в предыдущем случае, при отверждении меламиноалкидных ЛКМ одновременно протекают два процесса: испарение растворителя и поликонденсация смол (образование необратимой плёнки). В поликонденсации участвуют два компонента – но до поры до времени они мирно соседствуют в банке и друг дружку не трогают. Что это за компоненты? Во-первых, это алкидная составляющая, модифицированная растительным маслом, во-вторых – меламинформальдегидная смола.
В отличие от эмалей воздушной сушки алкидная составляющая меламиноалкидных эмалей содержит мало двойных связей, но обязательно имеет реакционноспособные гидроксильные группы ОН, как у спирта.
В отличие от алкидных эмалей алкидная составляющая здесь практически не вступает в реакцию с кислородом воздуха. Но зато при повышении температуры упомянутые гидроксильные группы ОН начинают взаимодействовать с метилольными группами меламиноалкидной смолы. Вот она, изюминка! Реакция между двумя компонентами запускается при нагреве! Поэтому второе название меламиноалкидных эмалей – «эмали горячей сушки».
Внимательный читатель уже, наверное, догадался о преимуществах такого механизма: в отличие от кислородного отверждения алкидных эмалей полимеризация здесь проходит равномерно по всей глубине. В результате образуется надёжная необратимая плёнка с пространственной сшивкой по всем направлениям. Если же равномерность отверждения вглубь слоя отсутствует, это означает одно из двух: либо эмаль «левая», основанная на дешёвом алкидном ингредиенте (в результате инициативу перехватывает кислород воздуха), либо нарушен температурный режим (реакция не пошла).
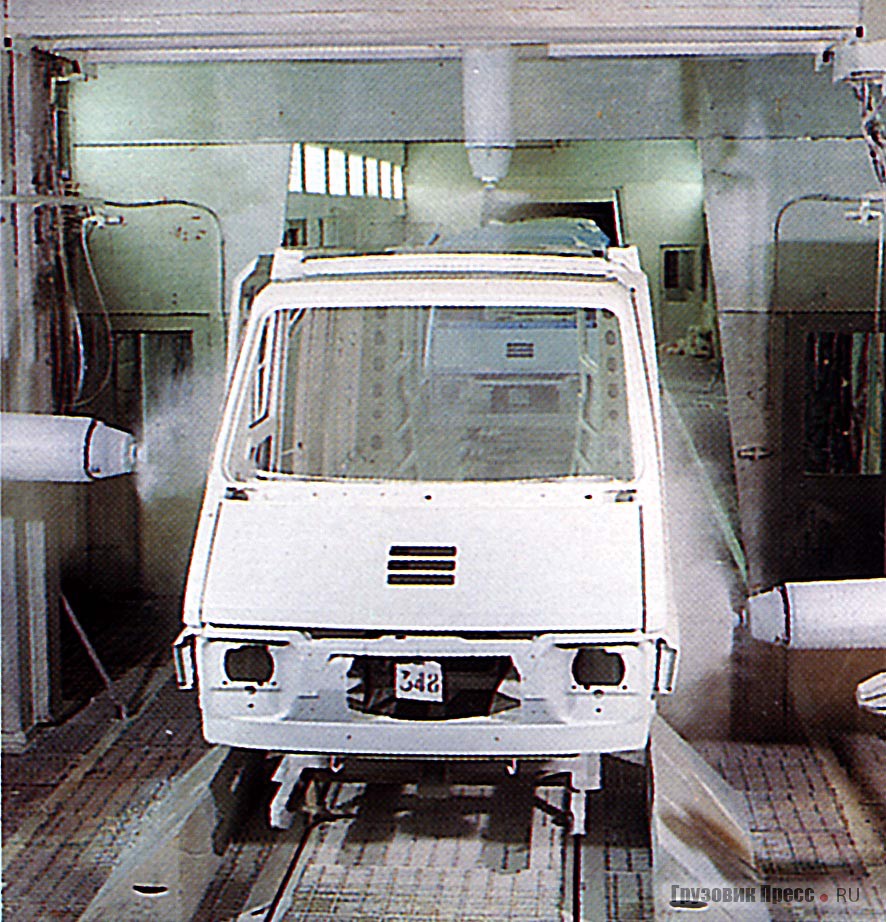
Итак, при высокой температуре меламиноформальдегидная смола играет роль отвердителя. А каковы значения этой температуры? Никакого секрета: 150 °С – для грунтовок, 130 °С – для эмалей, например, для широко известной МЛ-1110.
Впрочем, существуют эмали с отверждением при 105 °С. В них применяется более реакционноспособная меламинформальдегидная смола – она-то и позволяет снижать температуру сушки. Но есть у таких ЛКМ и минусы – хранить их более года нельзя, поскольку даже при обычной температуре реакция хоть медленно, но протекает. Это своеобразная плата за повышенную реакционную способность смолы.
Меламиноалкидные эмали применяют для окраски автомобильных кузовов на заводских конвейерах. А вот в ремонтных целях их используют в соответствии с поговоркой «на безрыбье…».
Акриловые эмали
Не ищите в химических справочниках и энциклопедиях слово «акрил» – все равно не найдете. Этот термин является разговорным и означает «акриловый лак», «акриловая эмаль». Но прежде чем коснуться теории, посмотрим на тару, в которую разлиты акриловые ЛКМ.
В этой группе материалов компоненты связующего (плёнкообразователя) разнесены по разным банкам. В отличие от меламиноалкидных эмалей хранить их в одной ёмкости нельзя, они тут же вступят в реакцию. Первый компонент содержит раствор акрилового сополимера. Это высокомолекулярное вещество, продукт совместной полимеризации акриловых мономеров – акриловой и метакриловой кислот, а также их сложных эфиров (если кому интересно – метилакрилата, бутилакрилата, метилметакрилата, бутилметакрилата и др.). И что важно: в составе этого сополимера есть звенья с гидроксильными группами ОН – запомним это.
Теперь о втором компоненте, фактически – отвердителе. В его состав входит полиизоцианат. Но название названием, а нам важно знать, что он содержит изоцианатные группы O=C=N-, весьма и весьма реакционноспособные. И когда раствор сополимера и отвердитель соединяют, гидроксильная и изоционатная группы вступают в реакцию. Благодаря этому возникающая при полимеризации полиуретановая сетка получает пространственные сшивки.
В конечном итоге в отверждённой акриловой плёнке образуется полиуретан, придающий покрытию исключительно высокие потребительские свойства, в частности стойкость к атмосферным воздействиям и эластичность.
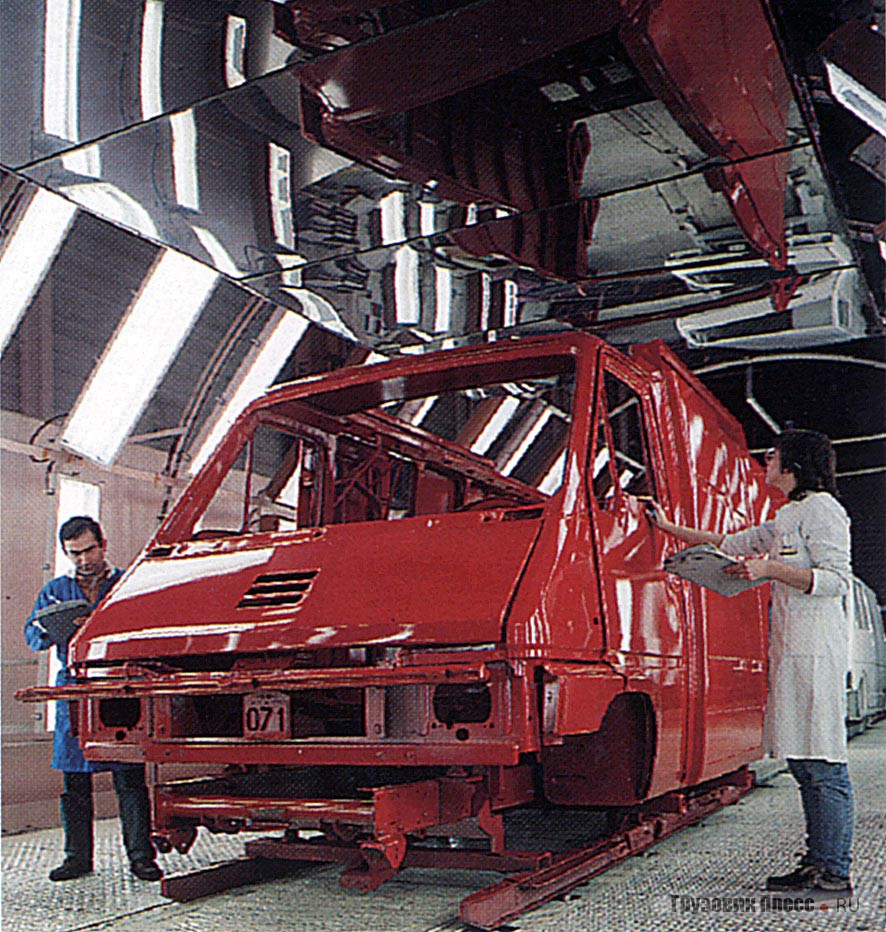
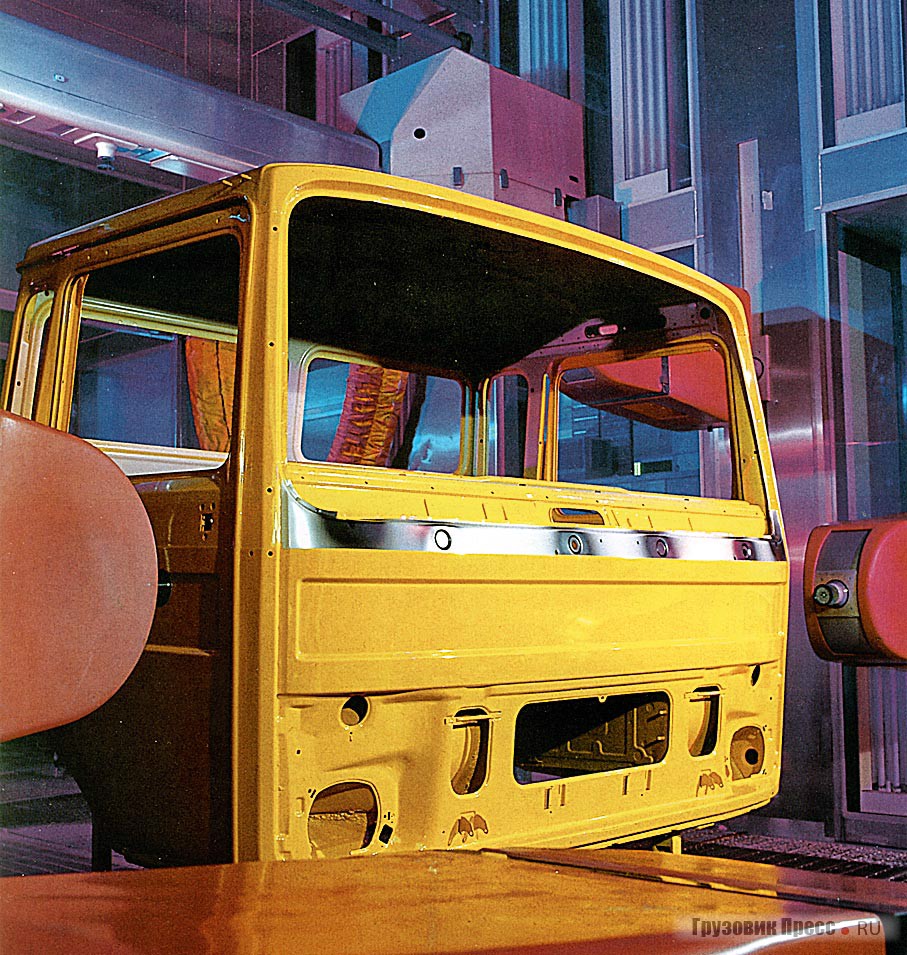
Описанная система носит название «акрил-уретановой». Такие материалы имеются в арсеналах всех известных окрасочных систем, как конвейерных, так и ремонтных.
Маляры-практики иногда спрашивают: можно ли разбавлять акриловые ЛКМ отечественными растворителями серии 645-651? Ни в коем случае! Отечественные растворители содержат спирты, а следовательно, посторонние гидрокильные группы ОН. Они способны направить реакцию по ложному пути, в результате чего пространственно сшитый полимер не образуется. По той же причине в системе недопустимо присутствие влаги. Следует применять растворители или разбавители, рекомендованные производителем ЛКМ.
Бывает и такой вопрос: можно ли отверждать акриловые ЛКМ изоцианатами, применяемыми в работе с меламиноалкидными эмалями? Нельзя! В акриловых системах сополимер и полиизоцианат тщательно подбираются друг к другу. Если взять другой отвердитель, получим другой полимер с совершенно иными свойствами.
Водорастворимые эмали
На рубеже веков человечество в хорошем смысле зациклилось на охране окружающей среды, озоновых дырах и глобальном потеплении. Тогда же в лакокрасочном мире родились два направления, позволяющих сократить выбросы ЛОС при производстве ЛКМ.
Первое – это материалы с высоким содержанием нелетучих веществ (вплоть до 100%). Наибольшее развитие они получили в Северной Америке*, именно оттуда пришло понятие HS (High Solid). Эта аббревиатура относится к ЛКМ, при нанесении которых в окружающую среду выделяется не более 420 г ЛОС на литр готового продукта.
Второе направление – это ЛКМ на водной основе. Наиболее интенсивно оно развивалось в Европе, а теперь становится господствующим во всем мире, включая Китай. В автомобилестроении первыми ЛКМ на водной основе были так называемые «окуночные» и анафорезные грунтовки. Кстати, в России такие материалы начали применять более 40 лет назад.
Затем на водной основе стали выпускать выравнивающие грунтовки и базисные эмали. Наибольший выигрыш по сокращению выбросов ЛОС даёт применение водных базисных эмалей, что понятно: в органоразбавляемых (мастера говорят – «сольвентных») базисных эмалях растворителей больше всего.
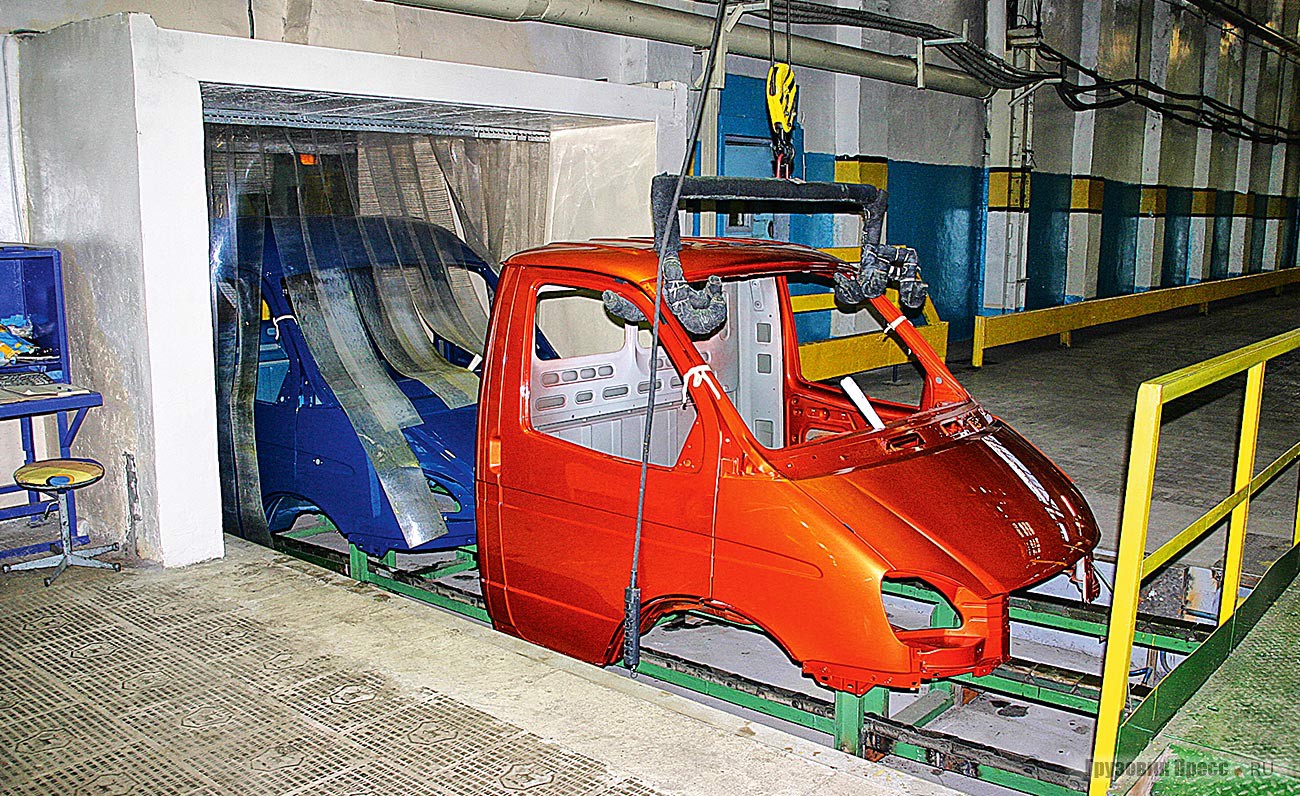
Общие принципы отверждения водоразбавляемых ЛКМ в общем-то те же, что и органоразбавляемых: физическая сушка и химическая реакция. Водные материалы существенно дороже органоразбавляемых. Правда, в Европе иной менталитет, экологический: «Я покупаю дорогой автомобиль, производство которого нанесло минимальный ущерб окружающей среде». Нам этого не понять. В Россию технологии нанесения водоразбавляемых ЛКМ не поставляются даже на автозаводы зарубежных фирм. Исключение – грунтовки. Что мешает? Законодательство, бедность, морозы? Ведь водорастворимые ЛКМ боятся холодов… Однозначного ответа нет.
Что касается своих разработок… Российские чиновники, предприниматели, инженеры и химики созданием отечественных ЛКМ на водной основе для автомобилей не озабочены. Значит, жизнь не заставила. Пока… не заставила.
Такова краткая ретроспекива развития автомобильных эмалей. От обратимой плёнки «нитро» через отверждаемое кислородом покрытие алкидных ЛКМ, через пространственную сетку «синтетики» к полиуретановой «сшивке» акриловых эмалей… «Нитро», «синтетика», «акрил»… И вот теперь – водорастворимые эмали, сохраняющие окружающую среду. Но нет предела совершенству. Пройдет немного времени, и появятся новые окрасочные материалы и технологии. И тогда мы опять вернемся к теме.
Растворители и разбавители
Растворитель и разбавитель – это не одно и то же, хотя и тот и другой применяются для получения требуемой вязкости ЛКМ.
Растворитель – понятие фундаментальное, он служит для получения истиного раствора, в котором молекулы растворенного вещества располагаются равномерно.
Разбавители, применяемые в лакокрасочной промышленности, строго говоря, не обязаны что-то растворять. Их задача – понижать вязкость, не приводя к расслоению и коагуляции разбавляемого продукта. Поэтому разбавители могут быть и несовместимыми с разбавляемым материалами.
Иногда свойство несовместимости разбавителей оказывается полезным: нарушение родственности изменяет форму макромолекул ЛКМ, они как бы «поджимают лапки», что очень эффективно снижает вязкость продукта. Разумеется, такие разбавители не должны отрицательно влиять на процесс формирования плёнки, и тут всю ответственность на себя принимает фирма, производящая разбавитель.
Несмотря на каталожное наименование «разбавитель», некоторые фирменные продукты с физико-химической точки зрения являются все же растворителями.
Ацетон, являясь растворителем, не пригоден для снижения вязкости ЛКМ – он слишком летуч и не обеспечивает оптимального высыхания плёнки при испарении. В лакокрасочной промышленности он применяется в качестве компонента сложного растворителя или разбавителя.
Катализаторы, инициаторы, отвердители
В публикациях на тему ЛКМ часто путают понятия «катализатор», «инициатор» и «отвердитель». В действительности это разные материалы и механизм их действия различен.
Как известно из школьного курса химии, катализатор увеличивает скорость химической реакции, но сам в реакцию не вступает. В акриловых системах используют катализаторы на основе органических аминов, ускоряющих реакцию уретанобразования.
Инициатор в отличие от катализатора участвует в реакции, генерируя радикалы, расходуется (распадается) сам и в конечном итоге входит в состав полимера. Пример: второй компонент (тюбик) в полиэфирных шпатлевках содержит именно инициатор.
И, наконец, об отвердителях. Отвердитель – это полноправный компонент связующего. Он не является ни катализатором, ни инициатором.